Understanding the Importance of Disposable Face Mask Making Machines
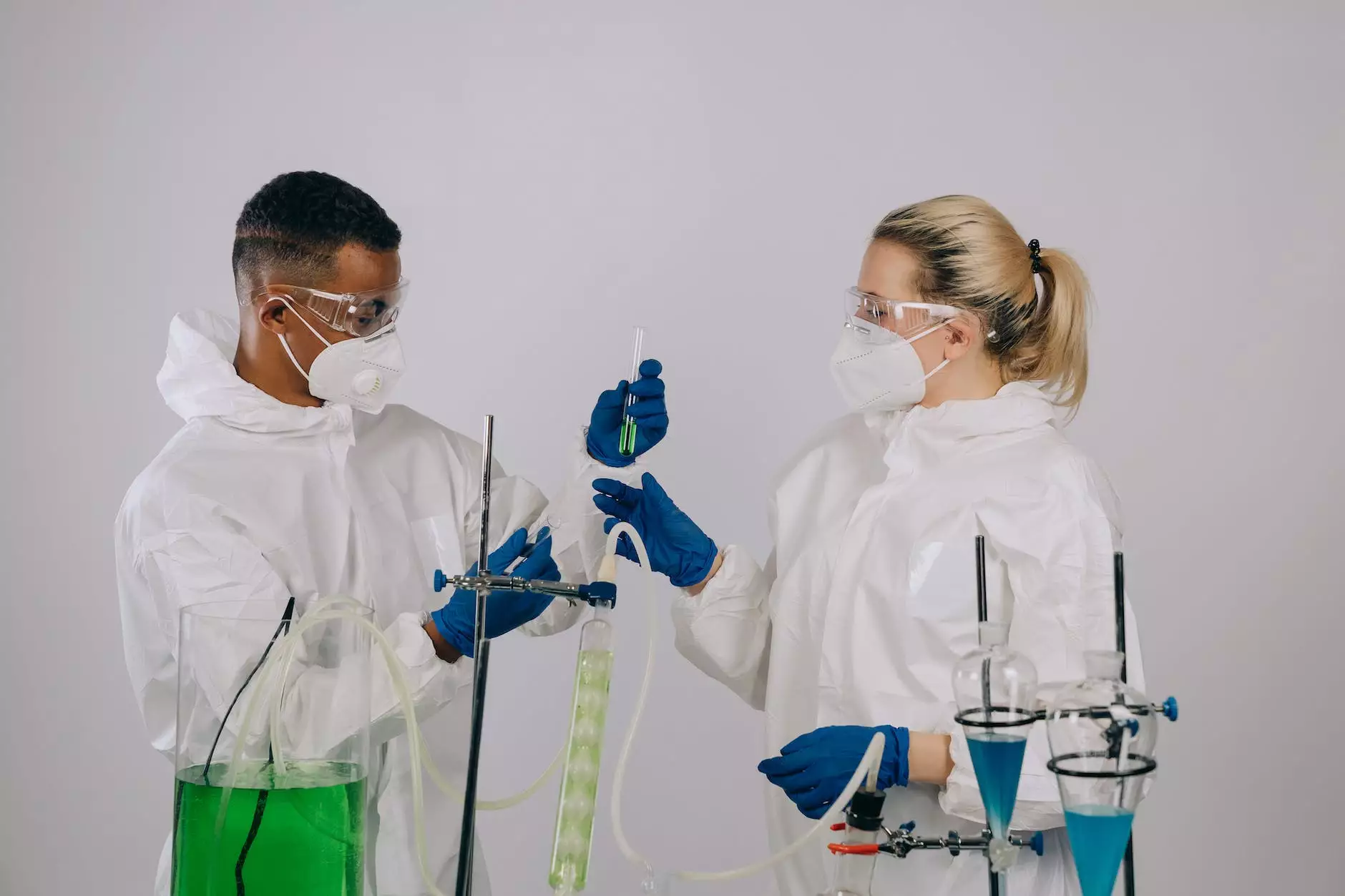
In today's global environment, the demand for disposable face masks has surged significantly due to various health-related challenges. The introduction of disposable face mask making machines marks a crucial innovation in the manufacturing industry, ensuring that these essential products can be produced efficiently and at scale.
The Rise of Disposable Face Masks
With increasing awareness about hygiene and the spread of infectious diseases, the use of disposable face masks has become a standard practice worldwide. These masks play a vital role in preventing the transmission of viruses and bacteria, making them essential in medical, industrial, and public environments.
Health Benefits of Disposable Face Masks
Disposable face masks offer numerous health benefits, including:
- Reducing Transmission: Masks significantly lower the risk of respiratory droplets spreading illness.
- Barrier Protection: They provide a physical barrier against contaminants in the air.
- Ease of Use: Disposable masks can be worn easily and discarded after use, minimizing contact with pathogens.
How Disposable Face Mask Making Machines Work
The manufacturing process of disposable face masks involves several steps, which are efficiently executed by a disposable face mask making machine. Here’s a breakdown of the process:
1. Material Feeding
The process begins with the feeding of non-woven fabric materials into the machine. These materials, often made of polypropylene, are critical for ensuring the mask is both effective and comfortable.
2. Mask Formation
The machine utilizes a series of mechanical operations to slice, shape, and form the mask. This includes:
- Cutting: The fabric is cut into specific dimensions for mask layers.
- Folding: The fabric is folded to create pleats for better fit and filtration.
- Ultrasonic Welding: This process bonds the layers together, ensuring durability without the need for adhesives.
3. Ear Loop Attachment
After forming the body of the mask, the machine automatically attaches ear loops. This step is crucial for ensuring that the mask fits securely on the face.
4. Quality Control and Packaging
Once the masks are assembled, they undergo rigorous quality control checks to verify their efficacy and safety. After passing these checks, masks are packaged for distribution.
Benefits of Using Advanced Disposable Face Mask Making Machines
Investing in a disposable face mask making machine offers several advantages:
1. High Production Efficiency
With automated systems, these machines can produce thousands of masks per hour, drastically reducing production times compared to manual methods.
2. Consistent Quality
Automation ensures that each mask produced meets stringent quality standards, minimizing defects and variability in the product.
3. Cost-Effectiveness
By increasing production capacity and minimizing waste, manufacturers can significantly lower their costs per unit, making mask production more economically viable.
4. Flexibility
Modern machines allow for adjustments to produce different sizes, styles, and types of masks, catering to a diverse market.
Shineben Machinery: Leading the Market
At Shineben Machinery, we pride ourselves on providing state-of-the-art disposable face mask making machines. Our commitment to innovation and quality has positioned us as leaders in the industry.
Our Cutting-Edge Technology
Our machines are equipped with the latest technology, ensuring:
- Speed: Industry-leading production rates that can be customized based on demand.
- Durability: High-quality components that withstand rigorous use.
- Easy Maintenance: Simple operational designs that make maintenance efficient.
Supporting Accessories and Their Importance
In addition to disposable face mask making machines, Shineben Machinery offers a range of accessories that enhance production efficiency. These accessories include:
- Automatic Feeding Systems: Improve material handling and reduce labor costs.
- Quality Inspection Systems: Ensure that every mask produced meets quality specifications.
- Packaging Solutions: Provide automated packaging systems to streamline the distribution process.
The Role of 3D Printing in Mask Production
While traditional methods for mask production are effective, 3D printing technology represents a revolutionary advancement in customization and production flexibility. 3D printing allows manufacturers to quickly prototype and produce unique mask designs tailored to specific needs and preferences.
Advantages of 3D Printed Masks
Some benefits of incorporating 3D printing in mask production include:
- Customization: Easy modification of designs for enhanced comfort and functionality.
- Rapid Prototyping: Quickly test designs before full-scale production.
- Resource Efficiency: Use only the necessary materials, reducing waste significantly.
Future Trends in Mask Manufacturing
As the industry evolves, we anticipate several trends shaping the future of disposable face mask production:
1. Eco-Friendly Materials
With growing concerns for the environment, there is a push towards using biodegradable and sustainable materials in mask production. This transition not only addresses ecological concerns but can also appeal to environmentally-conscious consumers.
2. Enhanced Filtration Technologies
Advancements in material science are leading to better filtration technologies that increase the effectiveness of masks against pathogens while maintaining comfort and breathability.
3. Smart Masks
With the rise of IoT (Internet of Things), there is potential for developing smart masks that can monitor health metrics, including air quality and breathing patterns, providing users with valuable data.
Conclusion: The Future of Disposable Face Mask Production
The importance of disposable face masks in today’s society cannot be overstated. As we navigate through current health challenges, the demand for innovative solutions in mask production is greater than ever. At Shineben Machinery, we are committed to leading the way with our advanced disposable face mask making machines, ensuring that manufacturers can meet the growing demand effectively.
By continually investing in technology and exploring new materials, we aim to provide our clients with the tools they need to stay ahead in the market. Embrace the future of mask production with Shineben Machinery, where quality meets innovation.