The Power of Injection Molding in the Automotive Industry
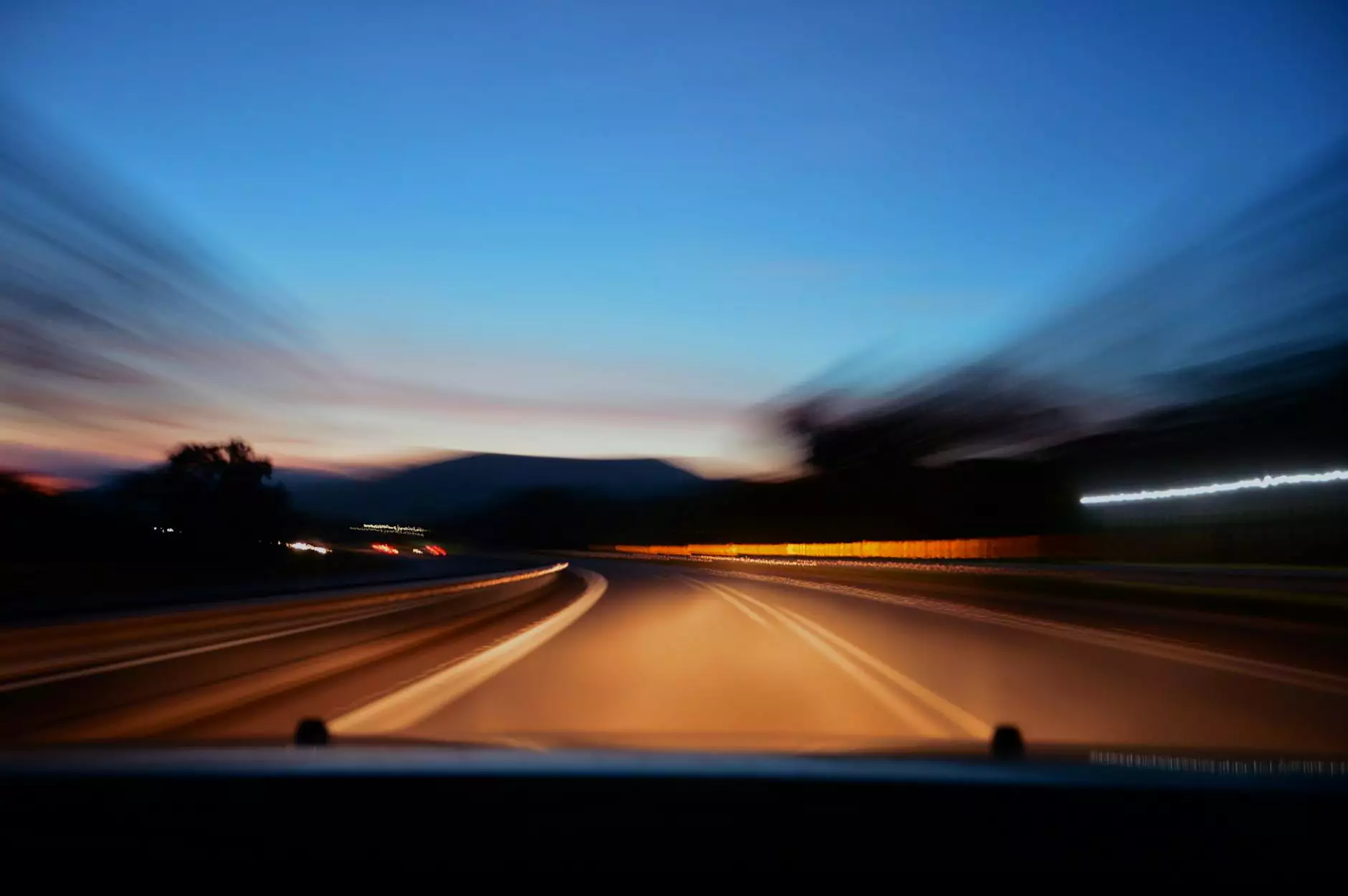
Injection molding has revolutionized the manufacturing landscape, particularly within the automotive sector. This state-of-the-art technique allows for the mass production of high-quality, durable parts that meet the rigorous demands of the automotive industry. In this article, we will delve into the world of injection molding automotive, exploring its benefits, applications, and the future of this technology.
Understanding Injection Molding
At its core, injection molding is a manufacturing process used for producing parts by injecting molten material into a mold. This process is highly efficient for creating complex shapes that would be challenging or impossible to produce with traditional manufacturing methods. The materials commonly used in automotive injection molding include various types of plastics such as ABS, polypropylene, and polycarbonate, making it a versatile choice for manufacturers.
Benefits of Injection Molding in Automotive Manufacturing
- Cost-Effectiveness: Injection molding is highly efficient, minimizing waste and reducing production costs, making it ideal for large-scale manufacturing.
- High Precision: This technique allows for the creation of complex geometries with tight tolerances, ensuring parts fit perfectly in vehicle assembly.
- Material Versatility: A wide range of materials can be used, allowing automotive manufacturers to select the best option for their specific needs.
- Consistent Quality: With automated processes, injection molding offers consistent quality across all produced parts.
- Reduced Lead Times: Parts can be produced quickly, decreasing time-to-market for new vehicle models.
Applications of Injection Molding in the Automotive Industry
Injection molding is prevalent in a variety of automotive components and systems. Some notable applications include:
1. Interior Components
Many interior parts, such as dashboards, consoles, and trim, are produced using injection molding. This process allows for intricate designs and textures that enhance aesthetics while ensuring durability.
2. Exterior Parts
From door panels to bumpers, exterior components benefit significantly from injection molding's ability to deliver high-strength parts that can withstand environmental factors.
3. Engine Components
Injection molding plays a critical role in producing engine components such as intake manifolds and covers, where precision and heat resistance are essential. Advanced materials are often used to withstand high temperatures and pressures.
4. Electrical Housing
The automotive industry relies on injection molded plastic housings for electrical systems. These parts are designed to protect sensitive electronics while conforming to specific safety standards.
5. Fluid Reservoirs
Fluid reservoirs, such as fuel tanks and coolant tanks, are frequently manufactured using injection molding. This method ensures leak-proof designs and the ability to withstand various chemical exposures.
The Injection Molding Process
The injection molding process involves several key steps that contribute to its efficiency and effectiveness:
1. Material Selection
Choosing the right material is crucial for achieving desired performance characteristics. Factors such as strength, flexibility, and thermal stability must be considered.
2. Mold Design
Designing the mold is a critical step; it must be engineered to accommodate the specific shape and features of the part while allowing for easy ejection.
3. Injection
The heated material is injected into the mold at high pressure, filling all areas to ensure a complete shape.
4. Cooling
Once filled, the part is allowed to cool and solidify within the mold. This step is essential for maintaining dimensional accuracy.
5. Ejection
After cooling, the mold opens, and ejector pins push the finished part out. This process must be carefully optimized to avoid damaging delicate features.
6. Finishing
After ejection, parts may undergo additional processes such as trimming, painting, or assembly to meet the final specifications.
Innovation in Injection Molding for Automotive Applications
The automotive industry is continuously evolving, and so are the technologies and techniques used in injection molding. Here are some innovative trends reshaping the landscape:
- 3D Printing and Injection Molding: The integration of 3D printing for prototyping and mold design is speeding up the development cycles and reducing costs.
- Smart Injection Molding: IoT technologies are being applied in injection molding processes to monitor conditions in real-time, ensuring consistent quality and efficiency.
- Biodegradable Materials: As sustainability becomes a priority, manufacturers are exploring biodegradable plastics for injection molding, minimizing environmental impact.
- Multi-Material Injection Molding: This technique allows different materials to be injected into a single mold, creating complex parts that combine various properties.
Challenges in Injection Molding
Despite its advantages, injection molding in the automotive sector faces several challenges:
1. Initial Investment
The cost of developing molds for injection molding can be significant, making early investments crucial for cost-effectiveness in mass production.
2. Design Complexities
Designing molds for intricate parts requires expertise and precision. Miscalculations can lead to delays and increased costs.
3. Material Limitations
While the versatility of materials is a benefit, not all materials are suitable for every application. Understanding specific material properties is essential.
4. Time Management
While injection molding offers reduced lead times, setbacks in design or material sourcing can impact production schedules.
Future Trends in Injection Molding for the Automotive Industry
Looking ahead, several trends are poised to shape the future of injection molding within the automotive industry:
1. Increased Automation
The trend toward automation is expected to grow, reducing labor costs and increasing production efficiency.
2. Emphasis on Sustainability
With a global push for more sustainable manufacturing, the development of eco-friendly materials and processes will become increasingly important.
3. Customization
As consumer preferences shift toward personalization, injection molding techniques will evolve to offer more customization options without sacrificing efficiency.
4. Advanced Material Development
Research into high-performance materials that are lightweight yet durable will continue, allowing for improved fuel efficiency and performance in vehicles.
Conclusion
Injection molding is an indispensable part of modern automotive manufacturing, enabling the production of high-quality parts efficiently and effectively. As the industry continues to innovate and evolve, embracing new technologies, materials, and processes will be vital for staying ahead. Companies like DeepMould.net are leading the charge, offering expertise in metal fabrication and injection molding automotive applications. Understanding these dynamics will empower manufacturers to leverage injection molding for their growth and sustainability in an increasingly competitive market.
In summary, the intersection of innovation, efficiency, and demand for high-quality automotive components ensures that injection molding will remain a critical pillar of automotive manufacturing for years to come.