High Precision Plastic Injection Molding: Revolutionizing Manufacturing
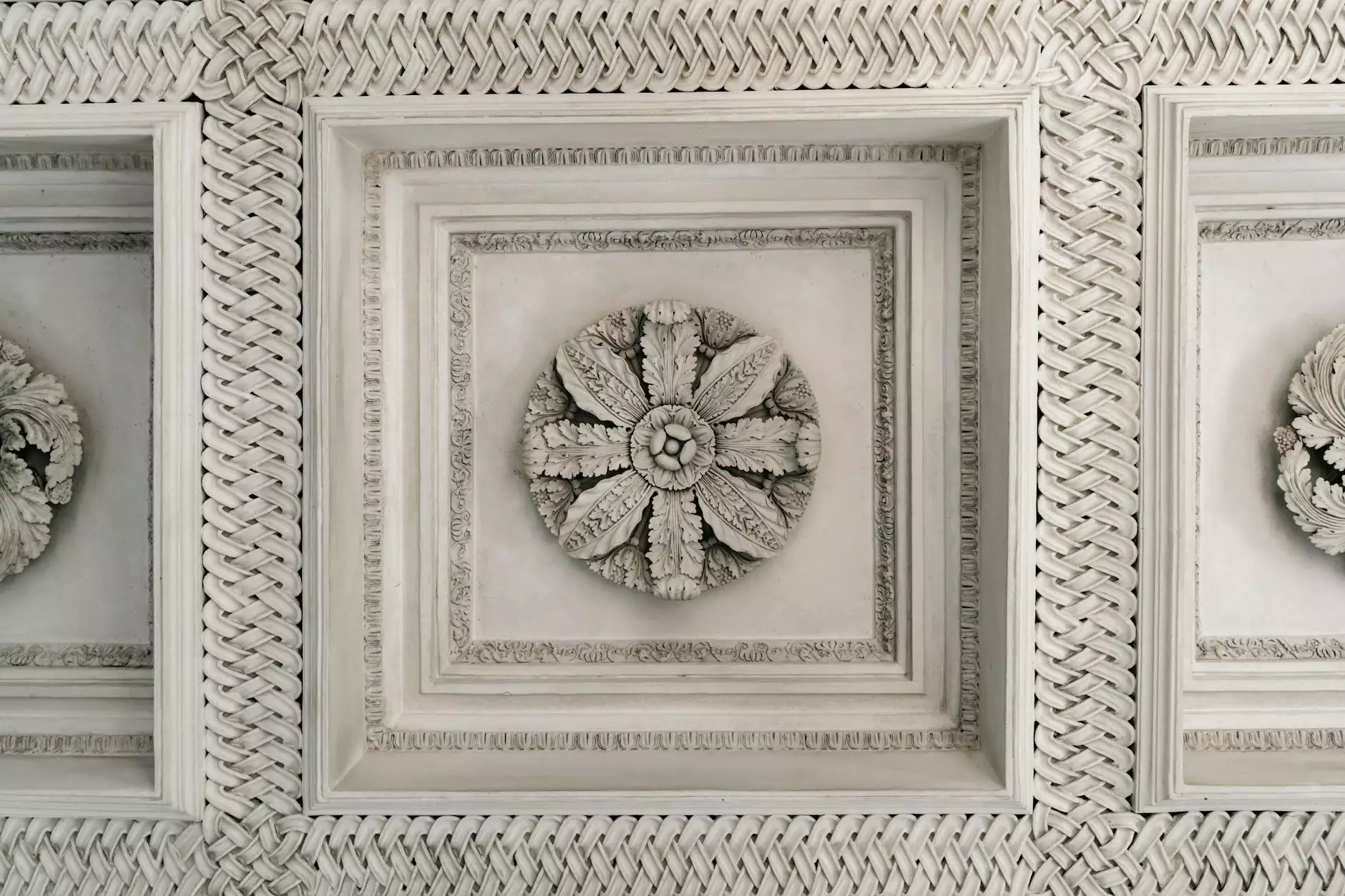
High precision plastic injection molding has reshaped the landscape of manufacturing across various industries. As a pivotal method in the production of plastic parts, it is lauded for its ability to create complex designs with high accuracy and repeatability. This article delves deep into the various aspects of this advanced manufacturing technique, shedding light on its significance and applications.
The Fundamentals of High Precision Plastic Injection Molding
At its core, high precision plastic injection molding involves injecting molten plastic into a mold to form specific shapes and designs. The precision aspect refers to the technology and machinery used, which ensure that parts are manufactured with minute tolerances. This process is essential in industries where accuracy and functionality are critical.
How It Works
The process of high precision plastic injection molding includes several key stages:
- Material Selection: Choosing the right type of plastic, whether thermoplastic or thermosetting, that will meet the requirements of the end product.
- Mold Design: Engineers create a mold that reflects the desired shape and specifications of the final product.
- Injection Process: Molten plastic is injected into the mold under high pressure, filling every detail of the design.
- Cooling and Solidification: The injected material cools and solidifies within the mold, taking its shape.
- Mold Removal: Once cooled, the mold opens, and the finished part is ejected.
Advantages of High Precision Plastic Injection Molding
The advantages of employing high precision plastic injection molding in manufacturing are manifold:
1. Enhanced Accuracy
Modern technology allows manufacturers to achieve extremely tight tolerances, which is critical for parts that need to fit within larger assemblies.
2. Efficient Production
Once the mold is created, producing parts is often faster and more efficient compared to other methods. This leads to higher throughput and reduced labor costs.
3. Material Versatility
A wide array of plastic materials can be used, enabling companies to select the best material for their product's performance and aesthetic requirements.
4. Waste Reduction
The injection molding process minimizes waste, as excess material can often be reused in future batches. This makes it not only more economical but also environmentally friendly.
5. Complex Geometries
High precision molding permits the creation of complex shapes that would be impossible or cost-prohibitive using traditional methods like machining or casting.
Applications of High Precision Plastic Injection Molding
Given its plethora of advantages, high precision plastic injection molding has found applications in various sectors:
1. Automotive Industry
In the automotive sector, components such as dashboards, interior trim pieces, and under-the-hood parts are frequently manufactured using this method, ensuring both durability and precision in the final products.
2. Medical Devices
Medical equipment often requires high levels of cleanliness and precision, making injection molding ideal for producing components like syringes and surgical instruments.
3. Electronics
From casings for smartphones to internal components of computers, precision molded plastics are indispensable in the electronics industry, providing the necessary protection and functionality.
4. Consumer Goods
Items like kitchenware, toys, and household products benefit from the aesthetic and functional attributes of high precision molds, reaching consumers efficiently.
5. Aerospace
In aerospace, lightweight and strong parts are critical. High precision injection molding produces components that meet rigorous standards of safety and performance.
Choosing the Right Partner for High Precision Plastic Injection Molding
When considering high precision plastic injection molding for your manufacturing needs, it is vital to choose the right partner. Here are some factors to consider:
1. Expertise and Experience
Look for companies with a proven track record and expertise in various sectors. The right partner will have experience in the specific challenges related to your industry.
2. Technology and Equipment
Ensure that your partner employs the latest technology and high-end machinery to guarantee the precision and quality of your parts.
3. Quality Assurance
A robust quality assurance process is essential to minimize defects and ensure that parts meet specifications consistently.
4. Customization Capabilities
Choose a manufacturer that can offer tailored solutions to meet your specific design requirements and material preferences.
5. Timely Delivery
Your partner should be committed to maintaining timelines, ensuring that your production schedule is adhered to without disruptions.
Future Trends in High Precision Plastic Injection Molding
The industry of high precision plastic injection molding is constantly evolving, driven by technological advancements and market demands. Here are a few emerging trends:
1. Automation and Industry 4.0
Incorporating automation processes and IoT technologies enhances efficiency and precision in manufacturing. This shift toward Industry 4.0 is reshaping how injection molding companies operate.
2. Sustainable Practices
With an increasing focus on sustainability, manufacturers are exploring eco-friendly materials and processes that reduce environmental impact without compromising on performance.
3. Advances in Material Science
Developments in polymers and composite materials will continue to expand the possibilities available through injection molding, leading to innovative applications.
4. Customization and Short-Run Production
As markets demand more personalized products, the need for quick turnaround on custom parts using high precision plastic injection molding will grow.
5. Enhanced Simulation Technologies
The use of advanced simulation tools for mold design and process optimization ensures better accuracy and helps in eliminating production errors before they occur.
Conclusion
In conclusion, high precision plastic injection molding stands as a cornerstone in modern manufacturing, offering unparalleled benefits in terms of efficiency, accuracy, and versatility. As industries continue to evolve, embracing this technology will become increasingly essential for businesses aiming to maintain a competitive edge. By understanding its intricacies and capabilities, companies like DeepMould can effectively leverage this powerful process to meet their manufacturing needs and drive innovation.